With company-wide ISO 45001 certification for occupational health and safety, we offer our employees a safe, clean, temperature-controlled working environment. Crucially, the volumetric system transfers high-risk work at height to the safety of the factory floor. Our units create safer homes too, with one example being that our projects offer 120 minutes of fire resistance, as standard.
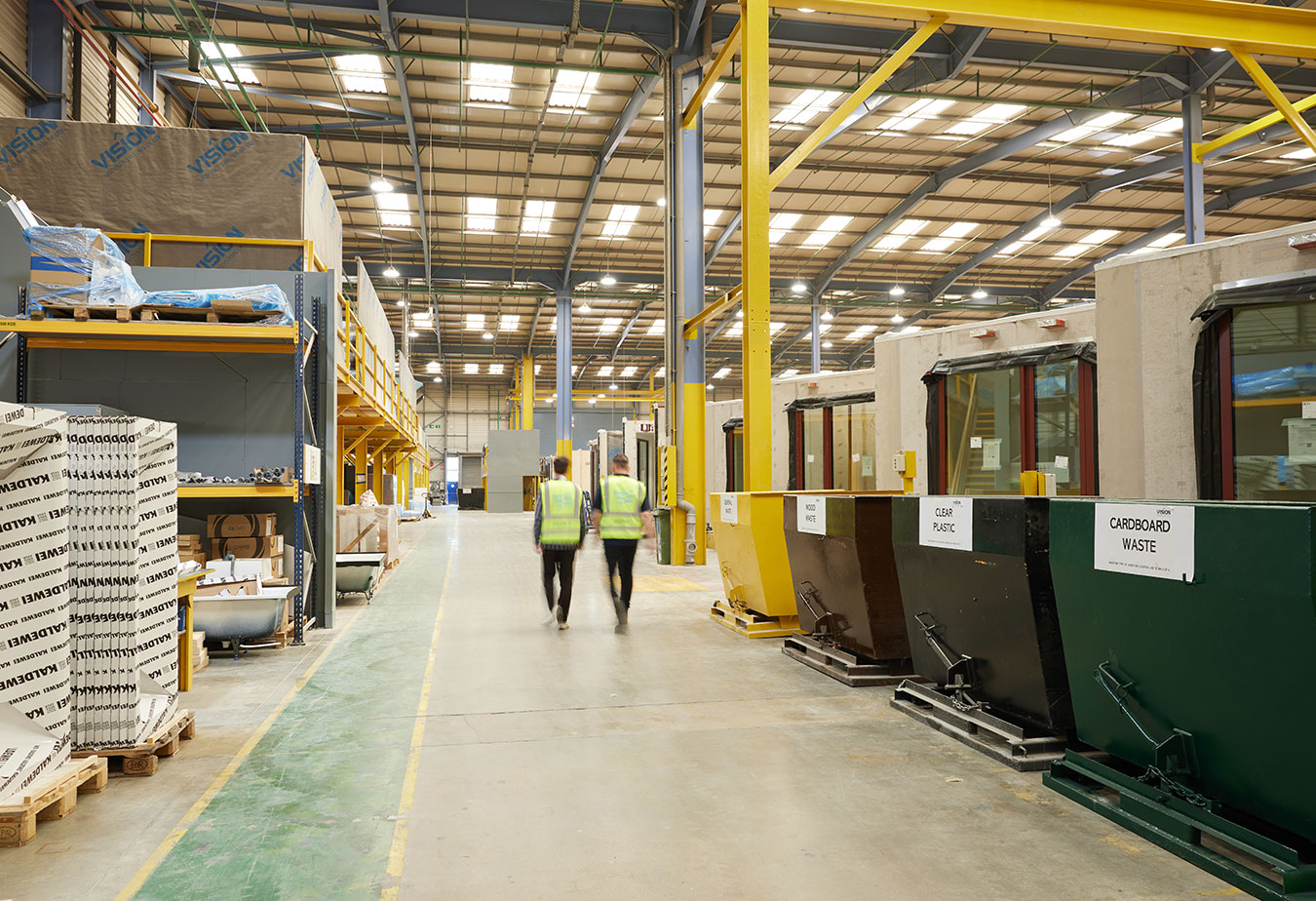